|
TOOLING DESIGN & DEVELOPMENT FOR A SHAFT TO REDUCE PROCESSING COSTS
Micro Metal Finishing has been applying plating to a wide variety of parts and components since the 1950s.
In a unique turnaround, an appliance industry customer asked them to design and develop tooling to keep the gear end of a shaft free of plating. Initially, the customer had been plating the shafts using their own operations, and using a labor intensive process to cap, plate, and then remove the caps to mask off the end of the part.
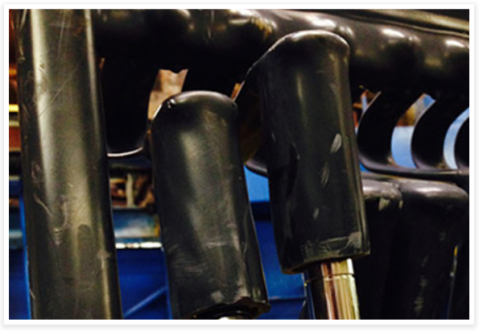
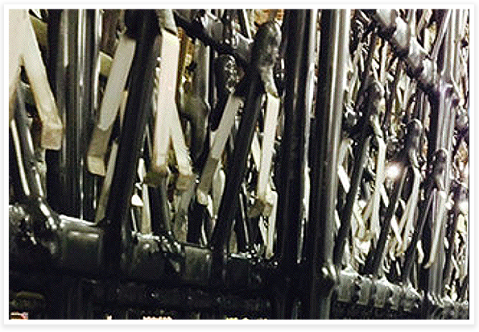
In a clear demonstration of the knowledge and creativity of Micro Metal's staff, we were able to offer the customer significant savings by designing custom racks to mask the shafts and eliminate the labor costs required to cap them. The unmasked area needed corrosion protection during transit which was then solved when we developed a custom rust preventive application process to protect the unplated ends of the shafts during shipping. Our plant manager, line leader, and outside tooling manufacturer worked closely to bring this project to fruition. The customer was so pleased with our production capability and quality that they eventually single sourced all of their plating requirements to Micro Metal.
Although this project may be unique, it serves as more than an anecdote of the customer service, engineering, and tooling creativity Micro Metal Finishing brings to any challenge with which we are confronted. Please contact us for further information.
PROJECT NAME
Tooling Design & Development
|
PROJECT DESCRIPTION
The end portion of a shaft had to be free of plating to protect the gear end of part from being plated.
|
CAPABILITIES APPLIED/PROCESSES
Primary:
Tooling Design & Development
Tooling Manufacturing
Secondary:
Plating
|
EQUIPMENT USED TO MANUFACTURE TOOLING
• Custom designed racks to mask off
• Development of oil application process
|
MATERIAL FINISH
Plated |
INDUSTRY FOR USE
Appliance |
|
|
|